In the terracotta world we speak about large pots when the measure could exceed 90 centimeters and 100 kg in weight. Of course, this is not an absolute discriminant. For example, if we consider just the industrial terracotta sector, certainly the 90 centimeters are an appreciable order of largeness. Speaking about handmade terracotta, those same centimeters become a normal thing, almost to indicate a medium-sized pot. Basically, a big pot is an object that impresses us for its size. We can see them in large spaces, such as shopping centers, airports or in important gardens. They are not common pots: in various aspects, both for the difficulty in production and for the prices, they are not for everyone. Not all manufacturing companies are designed for making them and the market is still thin for these oversized items. For the modest demand reason, there has not been such a great technical evolution in the production and these giants are for the most part made in Colombino technique, a construction system that is completely handmade where the craftman turns around his pot, and it is therefore difficult to have perfectly identical pieces.
Large pots, when exsists the conditions for recurrent production, can also be produced by special gypsum molds. Basically these are the pot shape negative, produced according to criteria deemed by the factory to be suitable to handle. To produce a 150 cm external diameter pot, which weighs approximately 350 Kg, is required a very heavy mold of 6-700 kg which, to be usable, has to be made in pieces that weight by according to the shape of the clay pot and the weight of the individual piece. This because, of course, everyone must be handled by the artisans. These and other aspects must be considered in the design phase of the mold, after which needs to handmade produce the original model, onto which the gypsum will then be cast. Normally, the mold for a round vase of 150 cm in diameter is made in three levels, a lower one for the bottom, a central one for the body and an upper one for the rim of the pot. Each level is at least 5 pieces each, so that the total weight between mond and clay is at most 25-30 kg and can be handle by the craftsman.
The first thing to do is to prepare for the bottom. So the five (or six) parts of the lower ring of the mold are assembled on a gypsum plain surface. Very important is that the plaster surface have to allow the heating/drying of the bottom in an artificial way. Normally inside that surface, serpentines are drowned and a hot liquid will flow, so that the top heats up. This is very important, as it will allow the large object to dry evenly and avoid possible cracks in the bottom. As soon as the lower part is assembled, proceed with casting the clay with the technique of the hand cast and so on, building up with the central part and the top of the pot. This operation, depending on the speed of the craftsman and the size of the pot, will take about 5-6 hours.
When we are required for large potteries generally they refer to objects of 60-70 centimeters and a few tens of kilograms of weight. In the large-scale retail trade, in fact, you will not easily find 140 cm in diameter and 250 kg in weight pieces. Most people do not know that these items are also found and which, to be honest, they are impressive.
Now needs to wait that the mold absorbs the water contained in the clay and allows the demoulding of the pot. Keep in mind that you are producing an object of over 400 kg, therefore the demoulding must first start from the top rim. Moving off the third ring parts will allow a faster drying of the central side and gives the artisan the way to adequately finish the rim. Generally 3-4 days elapsed, however dependent on the production season (in winter the time becomes longer) and after having valuated that it is dry enough to bear the weight of the top, the central part also is open. According to this procedure, it will be opened the lower ring and have only our large pot on the heated plain surface. But why do we proceed to artificially heat the bottom? This system allows a uniform drying and greatly reduces the chances of subsequent breakages in the bottom of the vase. To understand this step, imagine that when the clay pot is placed in the kiln to be fired, it will necessarily be uniformly dried, both at the bottom and at the top. During the drying phase, the water evaporates from the clay and we assist to a natural narrowing of the piece dimensions calculated in about 7-8% for the hand mold. This means that a 150 cm diameter terracotta pot when pre-fired is about 165cm. Imagine a shrinkage of 10-15 centimeters that does not occur evenly, because the piece is demoulded at different times. We have the bottom, which remains late in drying, the part at the top already in an advanced state of whitening and therefore quite immobile, while the lower part must necessarily shrink because it has to dry. This undergoes a force of resistance from above and therefore does not have other possibility than crack. If instead we artificially dry the bottom, this will go step by step with the rest of the pot and will not have so much need to retreat once in the drying room.
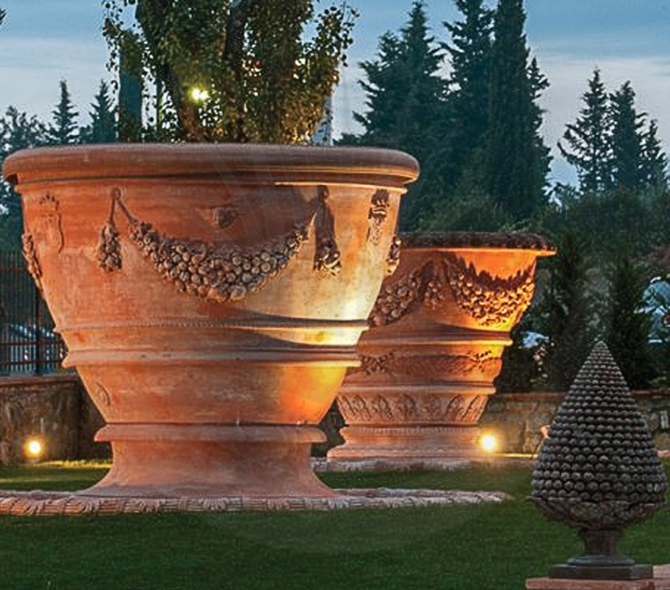
After, when the consistency allows it and the vase has sufficiently whitened (means dried),
the piece is moved into the drying room, taking particular care to avoid shocks in the
way. In this phase, in fact, the vase is very fragile and must be constantly monitored.
It normally stays for two rounds in the heat room - by round is meant the normal drying
cycle valid for smaller pieces - because the greater thickness requires a longer drying
time and finally, the pot is moved in the kiln for the firing. To fire large objects
is also a delicate phase, since the weight of the vase, is discharged itself in the laying
points, can cause breakages, especially on the bottom.
Certainly, the large pots are a big
challenge for the factories, both because of the objective production difficulties and because
they can hinder a lean production cycle typical of mass production, so just few
artisans are dedicated to this niche. Big Pots production, however, represent a note of value and
tradition,
which artisans are proud of because, in some way, that's a sign of high professionalism
and knowledge of their job.
I am curious