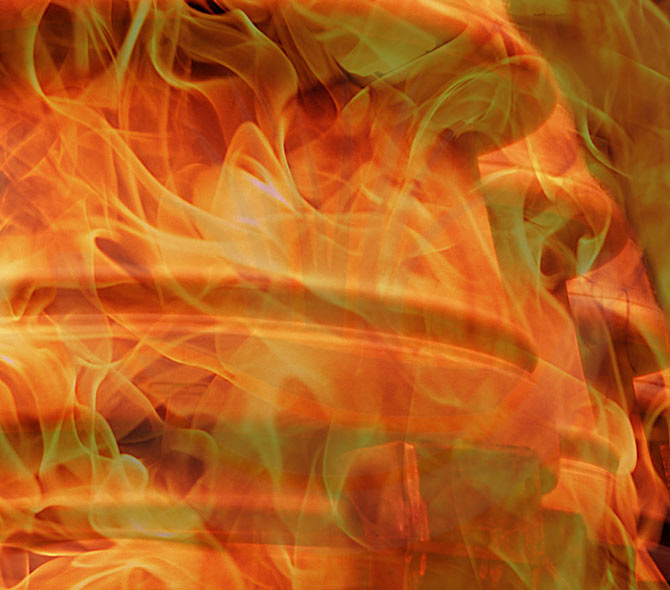
To obtain that hard and resistant red/rosy material, which does not exist in nature, humans learned to fire the clay that they had available, by long processes of exposure to fire. This process, known as the clay firing cycle, is a delicate process of applying heat energy that requires considerable experience, otherwise the object we want to produce will break. The result of the transformation is another material different from fragile clay, called terracotta.
For our purposes, we will focus on the firing cycle of garden terracotta, because as it is known, in addition to the noblest purposes of using the new material,
it was discovered that thanks to the properties of porosity and transpiration, terracotta was an excellent material for containing and allowing plants to thrive.
You can read more about this at healthy plants in terracotta pots.
The firing is one of the stages of the production process of garden terracotta, which, in order, are: preparation of the clay mixture, creation of the artifact, drying, firing,
wetting/cooling, and packaging. Just before firing, there is the necessary drying phase of the pot, because the clay mixture contains water in order to be
workable, and before proceeding with firing, the product must be completely dry. This step is intuitive if you have a basic understanding of physics:
water boils and transforms into steam, increasing in volume when it reaches 100 degrees Celsius, which is a very low temperature compared to the 1000 degrees Celsius required
to fire the clay. This means that if the pots to be fired still contain enough water, it will tend to evaporate and forcefully exit the object being fired at around 100-130
degrees Celsius, and will certainly cause the piece to crack. However, even the most effective drying cannot completely dry the pot, which still has a small percentage of
water inside, especially in pieces of great thickness. By the way, this does not pose a problem for the future integrity of the artifact, because the small amount of water
is able to exit through the pores present in the clay.
It's already clear from this explanation that the initial stage of firing, called tempering, must be conducted very slowly to allow the water to escape in
the form of steam from the tiny pores in the clay.
The firing cycle of garden terracotta is different, intuitively, from that of bricks (which have small thicknesses) or small ceramics.
It is clear that as the thickness of the product increases, the firing cycle must be longer in terms of time.
Generally, to fire a large vase, a cycle of about 34 hours is required.
At each transformation of the clay, understood as a possible shock to the artifact, it must be carried out slowly,
and then accelerated with fire until the next transformation is reached.
The first tempering phase, which goes from room temperature (let's assume 10 degrees) to 125 degrees,
precisely for the reasons just discussed, can take 7-8 hours.
In this long period, water has time to evaporate and come out of the pores in a soft way,
without causing cracks or explosions of the object.
Between 300 and 900 degrees Celsius, clays undergo the most important physical transformations:
The second critical phase occurs around 300 degrees, where the chemical water present in the particles is eliminated.
This phenomenon is called sintering, where clay particles create a stronger bond and therefore greater mechanical resistance.
Between 450 and 700 degrees, all organic substances present in the clay are eliminated. The zone around 580 degrees is particularly important,
where the process of silica particle inversion from alpha to beta occurs. It is a reversible process in the sense that such particles
return to alpha when the temperature falls below 580 degrees and can cause increases in volume that could generate microcracks, so in this
third delicate phase, caution is necessary.
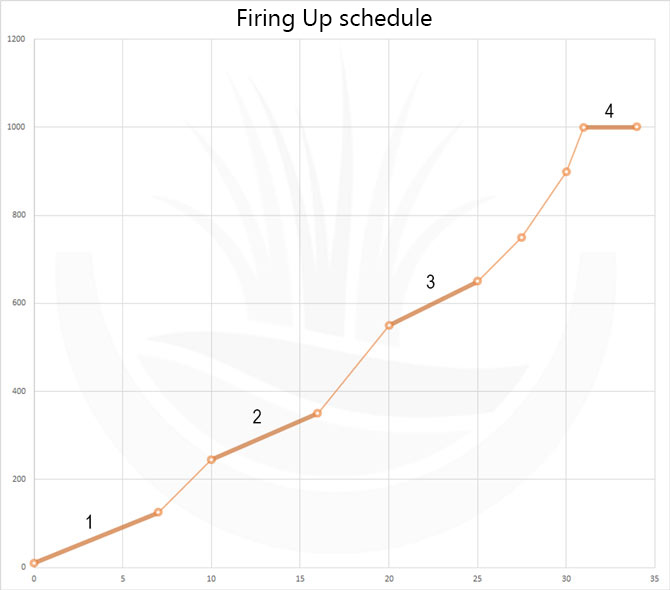
The last noteworthy phase in the clay firing process is the so-called maturity or stabilization phase. Essentially, once we have reached the
highest possible temperature, beyond which the clay is melted, we regulate the heat tuning to stop rising and maintain the maximum temperature for about 3-4 hours
(depending on the thickness of the material being fired). This way, the heat penetrates throughout the thickness of the object, giving it greater hardness and
robustness and contributing to ensuring its maximum durability and resistance to weather exposure. In addition, the maturation allows the fire inside the kiln to
descend towards the lower part of the kiln in order to fire well also the pieces that are at the base of the load. It is known that modern kilns are mostly turbofan
and therefore with inverted flame, and therefore the pieces that are last loaded into the kiln (those placed on the upper part of the load) are fireed first.
With stabilization, the hot mass is allowed to descend, firing the lower part as well.
The firing process physically transforms the clay mixture by applying an energy, in this case the fire. The molecules of the material modify their structure by changing into compact and hard solids. For good firing you need to know how to apply th fire energy to obtain a hard and long-lasting material. In the article we explain the firing process in the various phases
Once the firing process is completed, the burners are turned off and the oven chimneys are closed. The oven remains under
pressure and continues the natural maturation phase. New ovens, those that are not worn out and do not have
heat losses, could even shorten the phase 4 of maturation, as it could use the pressure phase time to complete the firing process.
Particular attention is also paid during the cooling phase to zone 5 at 580 degrees, where the conversion of quartz from beta
to alpha takes place, and in any case maximum attention is paid to sudden temperature changes at least until 200 degrees.
A highly efficient oven from the point of view of heat retention, without excessive vents and/or leaks, could also use the internal
heat as a recovery source for the drying room. Unfortunately, over the years, the ovens' tightness decreases, and often the
cooling phase occurs naturally.
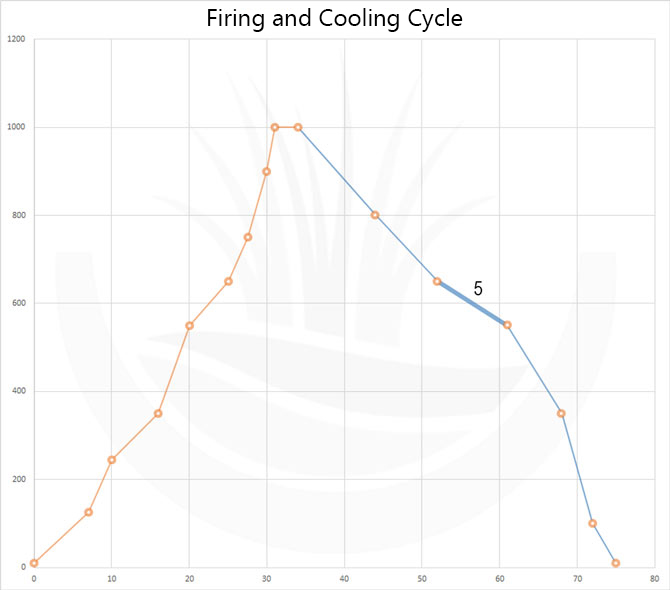
The experience and knowledge of the type of clay that we are going to fire and the tool used for firing (oven) allow us to calibrate optimal firing cycles to obtain a quality product that is resistant and durable, as well as energy savings, which is an important cost source in every terracotta producing company.